At any given moment, over half the world’s population is wearing denim. This staggering statistic is a testament to the prevalence of our favorite indigo fabric across the globe – and the importance of creating it with as little impact as possible cannot be overstated. Earth’s finite resources are currently being stretched as consumption habits continue to rise. A solution is long overdue; Prosperity Textile’s could be the one we’ve been waiting for. On this World Water Day, let’s take a look at water, denim, and the reconciliation we’re seeing come out of some pretty innovative technologies.
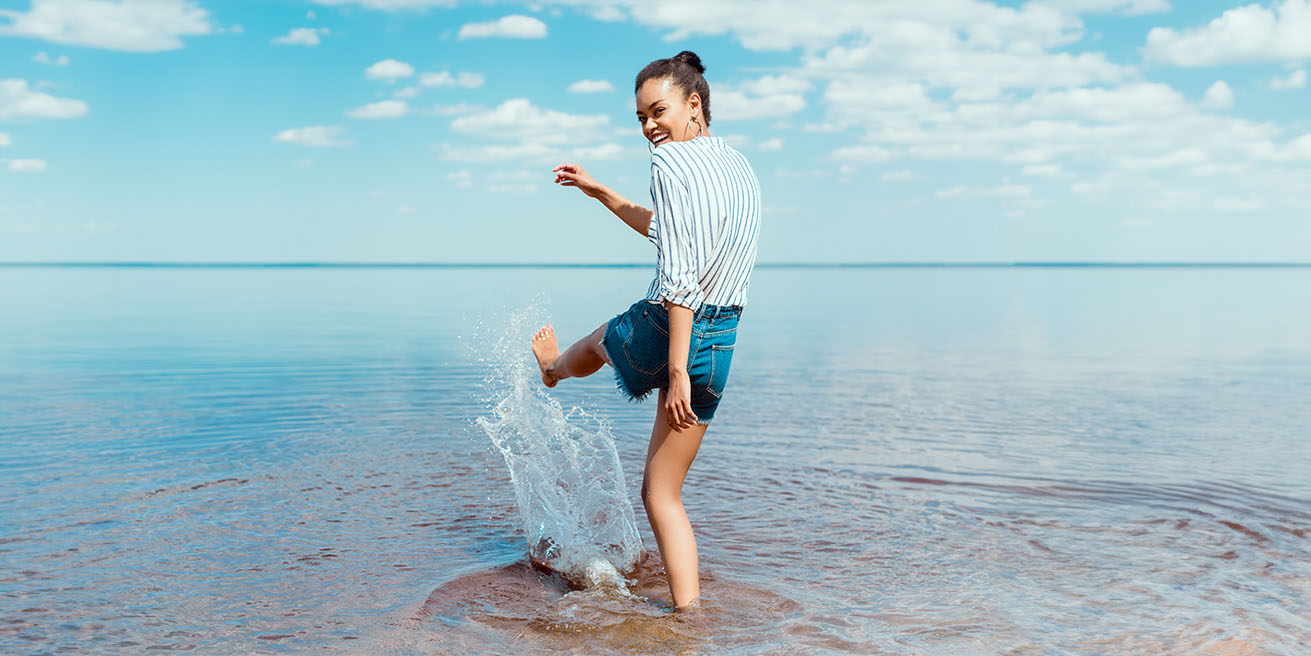
Traditionally, denim creation involves a polluting, resource-heavy process that uses the equivalent of about 150 bathtubs full of water to produce a single pair of jeans. This may come as no surprise given the fact that the fashion industry is the 2nd most water-intensive industry on the planet. And within the world of fashion, denim fabric is pretty much the top dog when it comes to high environmental impact.
Prosperity Textile has been working to improve water use in denim production for years. What began in 2002 as a small denim mill in China’s Guangdong Province has become a force in the industry with 1,900 employees in two locations: Vietnam and Shaoguan, China. As a bluesign® system partner, Prosperity is considered to be one of the cleanest mills in the world – and is continuously striving to decrease its impact on the planet.
A new production method for denim
As part of their sustainability efforts, Prosperity Textile has partnered with textile innovations company NTX and in November 2023, put their water-saving coloration technology Cooltrans to use. The NTX Cooltrans process facilitates the transfer of a denim design from film to fabric without the use of heat and with a more than 90% water use reduction by printing high-quality, realistic denim ‘images’ onto fabrics. Goodbye denim dyeing and hello denim printing – this version on fabric instead of paper.
“For the first time in 150 years of denim history, there’s a new way of creating denim without the use of indigo and laundry processes and still making it look great and authentic,” says Marco Stefanelli, Director of Marketing & Business Development at Stella Blu Textile, part of Prosperity Textile Group. “We’ve spent the last couple of years tweaking this process. We’re now able to fool even the most sophisticated denim gurus: when we put conventional denim in front of them next to denim made with this technology, they cannot see the difference.”
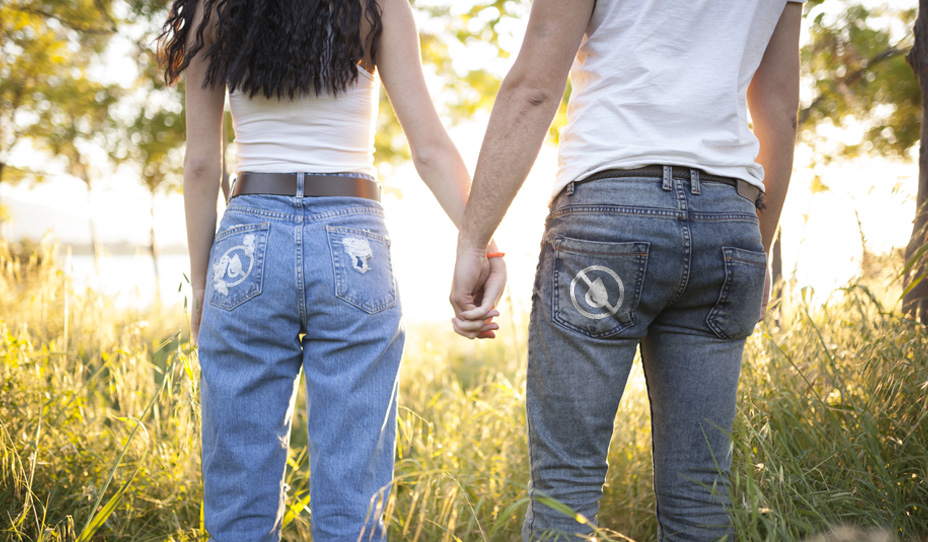
Printing magic at its finest
Cooltrans can be used on nearly any fabric, whether natural or synthetic. The process is incredibly precise and doesn’t compromise the fabric’s feel or performance. Now, denim brands don’t need to rely on fabric composition to achieve a certain look – they can decide exactly what they’d like on the fabric of their choice, meaning a huge cut in costs.
What’s more, NTX’s denim production technology is free from indigo dye and other harsh chemicals – which cause great environmental harm – adding another layer of sustainability to the creation of what seems to be the world’s material of choice.
The results of this printing process offer some significant savings: 90% less water is used; 65% less energy is used; and 40% less dye is used, among others.
The Higg Index (now Worldly) has weighed in on the Cooltrans innovation and named it as having the lowest impact on the environment of any coloration system in the fashion industry, beating out batch dye, screen print, continuous dye, and digital prints.
In comparing the water-saving methods adopted by Prosperity Textile to digital print processes, the latter can create inconsistencies due to the uneven structure on the surface of the ink. Due to its slow speed, digital printing is also not scalable to high volumes. Meanwhile, Cooltrans prints on a flat carrier, resulting in higher resolution, more consistent images at high speeds.
“We are the first denim mill to adopt the use of this technology,” says Stefanelli. “World-renowned brands are showing great interest and are moving into this with great conviction. Hopefully we can inspire other players from within the denim industry so that it can transition from indigo dyeing, laundry, and heavy washes and chemicals to address sustainability issues, reduce fabrics libraries, and increase speed to market.”
As for the price tag, it’s cost neutral. In other words, no more or less expensive than what’s already being paid for traditional denim production. Stefanelli says they’re planning to scale up production to 3 million yards per month by Q3 of this year.
Water and denim are inextricably linked. Since the first pair of jeans was created in the 1870s, water has played a major part in the creation of each pair – until now. As water scarcity becomes a problem for millions of people globally, the water footprint of the fashion industry is under pressure. This water-saving solution just might change everything.
Source water-saving denim in Best of Denim
Interested in adding denim fabrics made without water to your next collection? Find Prosperity Textile’s water-saving denim here and support the future of denim production on this World Water Day. Can you tell the difference?
Related content
Want to chat?
We’d love to hear from you. Reach out to see how we could work together.